联系电话:0755-28853708
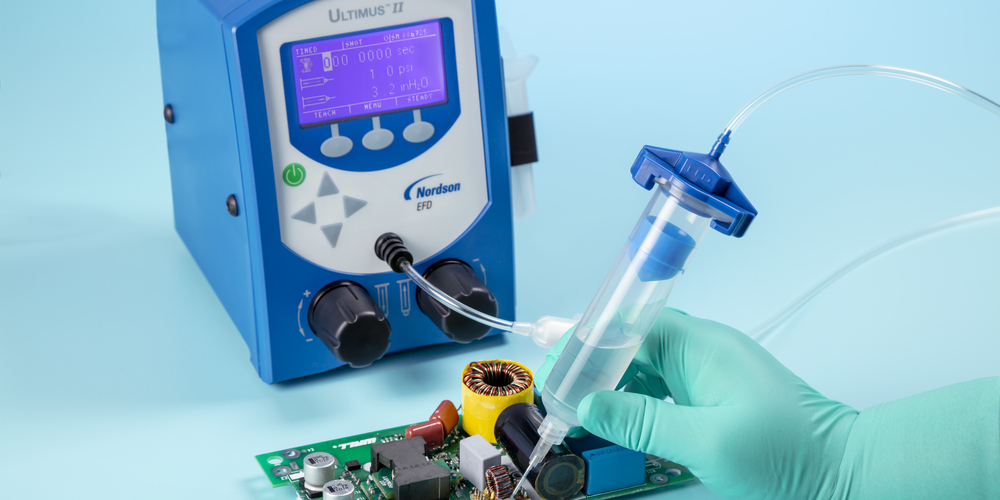
令人惊讶的是,尽管流体分配技术取得了许多进步,但超过 50% 的工业和制造工厂经常使用挤压瓶、医用注射器、棉签和牙签在其装配过程中涂抹流体。
这些调查由诺信 EFD 赞助而来。大约 290 家不同制造业的公司做出了回应。他们被要求对他们最常使用的分配方法进行排名。他们选择了从最常用到不常用的多种方法。根据调查,以下是最常用的流体分配方法:
· 58% 使用挤压瓶和医用注射器
· 51% 使用棉签和牙签
· 44% 使用 气动流体分配器
· 27% 使用 气动阀门系统
在这篇博文中,我们将讨论将点胶方法从基本的挤压瓶、注射器、牙签和棉签升级为精密气动台式流体点胶机的诸多好处。
一、使用流体分配器的好处
大多数制造商可能从手动挤压瓶和医疗针筒分配开始。 然后,随着产量的增加,在采用更可控的方法和精密台式流体分配器或气动阀系统至少部分流体分配方面取得了一些进展。
而其他人则走不同的路线——而不是升级——他们维持手动挤压瓶分配流程,增加更多的生产站和更多的工人来处理增加的数量。从生产能力的角度来看这两种方法,采用更有效和受控的流体分配方法有几个好处。 这里仅仅是少数。
1、逐次点胶的可重复性和准确性
与手动挤压瓶分配相比,气动分配显着改善。 根据研究的最新结果,逐次点胶的可重复性和准确性是受访者最渴望的两项改进。 沉积适量的流体具有保持下游生产移动的复合结果。 例如,如果使用过多的液体,固化所需的时间越长,这将延迟下游的生产。 相反,如果应用的流体太少,零件将无法正确粘合,再次中断下游组装或导致产品故障。
2、提高生产力
显然是一个好处 气动台式点胶 超过手动挤瓶过程。 例如,在 8 小时轮班中手动组装 800 个零件的同一工人可以在气动流体分配器的帮助下组装 1,000 到 1,200 个零件。 这是一个生产吞吐量增加高达 40%。
3、零件质量提高
当从手动挤压瓶分装切换到气动分装时,因为减少了操作员之间的差异。 为应用设置时间、压力和其他点胶参数的能力改善了过程控制并确保在每个部件上放置适量的流体。
4、返工和废品减少
升级到气动点胶时。 在一些电子技术行业和医疗器械工厂中,由于手动挤压瓶流体分配不良而导致的一个被拒绝零件可能会浪费数百甚至数千美元。
总而言之,尽管在组装过程中可能总是需要某种程度的手动挤压瓶分配,但在相当大一部分流体分配中严重依赖挤压瓶、医用注射器和牙签的制造商,无论其分配多么精确或不精确参数可能是,可以通过仔细研究它们的生产能力而受益匪浅。
在他们使用的方法和更精确的解决方案之间进行成本效益比较,例如 气动分配器 有帮助。 然而,考虑列出的五个点中的每一个点都至关重要,因为其中许多点代表了影响手动挤压瓶、牙签、拭子和医疗针筒分配过程的实际成本效益评级的隐藏成本。
(文章转自 诺信 EFD 官网)